Most Compact Actuator Suspension In Brick Rigs
Over sling or Under sling camera off the front or rear in minutes and fine tune the height with electronic actuators making camera height adjustments quick and easy. Built and tested to utilize a 3 axis stabilized head with a rig system pulling from the center of the bike to make riding easier with a more compact feel. Drives an actuator (linear or rotational). The pump used in hydrostatic systems is a positive displacement pump. The relative spatial position of this pump is arbitrary but should not be very large due to losses (must be less than 50 m). An example of pure hydrostatics is the transfer of force in hydraulics. Shock absorbers are one of the most important elements in a vehicle’s suspension system, and they play an important role in determining vehicle handling and ride characteristics. Depending on the application of the vehicle.
A low-profile, piezoelectrically-driven microactuator is presented that achieves very large stroke lengths within size constraints suitable for certain endoscopic microscopy applications. The actuator utilizes a transmission consisting of lever arm and chevron-beam structures to amplify high-force, low-displacement motion of a ceramic lead-zirconate-titanate (PZT) brick into large displacement of a translational platform. For ±120 V input, a full range of 486 μm of motion is achieved, with natural frequency greater than 500 Hz. This corresponds to an anticipated In addition, the lateral translational platform is supported by a redesign of common folded silicon flexures to provide large transverse and vertical stiffness when the width of the actuator is limited. IntroductionA silicon transmission coupled with a piezoelectric ceramic is designed and tested for large displacement actuation within endoscopic microscopy space requirements. Several types of novel imaging modalities enable deep optical penetration (up to 500 μm) into biological tissue , including dual-axes confocal microscopy and two-photon microscopy ,. Large, high-speed displacement of optical components such as mirrors or lenses via microactuation could rapidly change such microscopes’ depth-of-focus to produce real-time cross-sectional or three-dimensional images.One proposed endoscopic instrument is a two-photon microscope with its optical path occupying the center of the imaging system; actuators that fit along the side of the optical path minimize total cross-sectional area and volume of the scanning head used to generate images.
Such actuators would need a cross-sectional area of approximately 3 mm by 0.6 mm or smaller, and a length less than 20 mm, to avoid increasing scanning head size when implementing into-tissue scanning. Scanning range should be nearly 500 μm, at an unloaded frequency of at least 100 Hz. This corresponds to real-time scanning of 10 Hz or better when equipped with a 3 mm diameter, 0.12g focusing lens, and a projected optical scanning distance in tissue of 220 μm.The combination of stroke length and speed desired exceeds that demonstrated by previous miniature actuators of the size desired. For example, large displacement thermal actuator speed is limited by the thermal time constant of the devices and heat generated may be difficult to dissipate in vivo ,. Piezoelectric stack actuators and DC-linear motors used in previous miniaturized optical imaging systems do not meet the space requirements and would increase probe volume ,.
Electrostatic actuator mechanisms are well established for a wide range of stroke lengths , , but suffer from limited force side-instability at very large displacements.The actuator described here relies on the large work density of piezoelectric materials, and converts small-displacement, large-force motion of a lead-zirconate-titanate (PZT) ceramic into large displacement motion via a micro-machined silicon transmission. The actutator optimizes a combination of lever-arm and bridge-type amplification mechanisms. Both types of amplification have been previously used in micro-scale systems, such as , , and the optimized mechanism combining their effects shows amplification ratios exceeding those previously described for fabricated MEMS devices.
In addition, a folded flexure design is adapted from conventional arrangements to fit in the long but comparatively narrow space available for the two-photon microscopy application. To illustrate the benefits of this approach, compares the cross-section, displacement, natural frequency, and amplification ratios of existing large stroke or large amplification microactuators. Stroke ( μm)Cycle Freq. Mm × mm.AmplificationFaulhaber DC Linear150003006.8×6.8N/AHenderson Piezo wiggle600050001.6×1.6N/ASmith et al. Modified comb500unreported3×0.1N/AHubbard et al. Thermal522302.5×13.5xConway et al.
PZT1.450000.5×0.5410xKota et al. Comb drive203880. Transmission DesignThe ability to perform endoscopic tissue imaging using a fiber-coupled two-photon laser has recently been demonstrated by several research groups as ,. For many applications the size of the scanning mechanism for image creation is a limiting factor in system miniaturization. Many projects concentrate on automated x- and y- scanning, but a fast enough scanning mechanism parallel to the optical path could ultimately lead to 3-dimensional imaging of tissue structures in vivo, with novel diagnostic capabilities for allergic diseases and cancer. Shows the schematic drawing of a scanning probe suggested by the Biomedical Research Team at the University of Michigan; a MEMS mirror unit performs x- and y- direction scanning, while a large displacement linear actuator drives a lens to adjust the focal depth during scanning. Schematic drawing of a 3-dimensional scanning two-photon endoscope with an x- and y- scanning mirror and a focusing lens.We suggest a linear actuator design consisting of three parts: a piezoelectric material to generate a motion, an amplification structure that uses lever-arm and chevron bridge-structures to transform the motion and a platforms that allows the fixation and stabilization of a micro-lens.
Illustrate the first amplification stage. Two short, parallel flexures are placed a small distance apart, one connecting a lever-beam to a fixed base and the other connecting the lever-beam to a nose that is actuated by a piezo (piezo not shown in this illustration).
Using the lever-effect the lateral displacement of the piezo is transformed into a large transverse displacement of the two lever-tips. As shown in c), the transverse movement of the lever-tips is then re-transformed into a lateral movement of the amplifier-tip using a second, chevron bridge-type amplification structure. (5)where T matrices include small displacement moment arm lengths to perform moment balance calculations.The system of linear equations provided by and may be solved to relate piezoelectric ceramic force and displacement, F 0 and X 0, to platform displacement, X 6 against a load force, F 6.In particular, x-displacement of the platform, x 6, is obtained when transverse and rotational motion of platform and piezoelectric ceramic ( y 6, θ 6, y 0 and θ 0) are constrained to zero by symmetry.
In addition, the relationship between the piezoelectric displacement, x 0 and the opposing lateral force on the piezoelectric actuator, F 0, are related using piezoelectric strain coefficient, d 3,1, to be. (6)where V is applied voltage, t PZT, L PZT, A PZT and E PZT are thickness, length, cross-sectional area, and elastic modulus of the PZT ceramic.The full analytical model agrees with finite element models, save for slight overstatement of platform deflection ( 10%) due to the neglect of any deformation in the long lever arms. Linear simulations were also compared to nonlinear simulation results, with only small differences, as shown in. Likewise, stress within the flexural beams was calculated from the intermediate forces in the system equations, again with close agreement to full finite-element simulations, permitting design optimization with maximum stress limits. Platform Suspension DesignIn an endoscopic imaging system, two parallel piezoelectric linear actuators drive the focusing lens resting on the moving platform. The typical lens mass approximates 20 mg. Thus, a suspension system with a low spring constant in the actuation (lateral) direction and a high spring stiffness in the vertical and transverse direction is required.
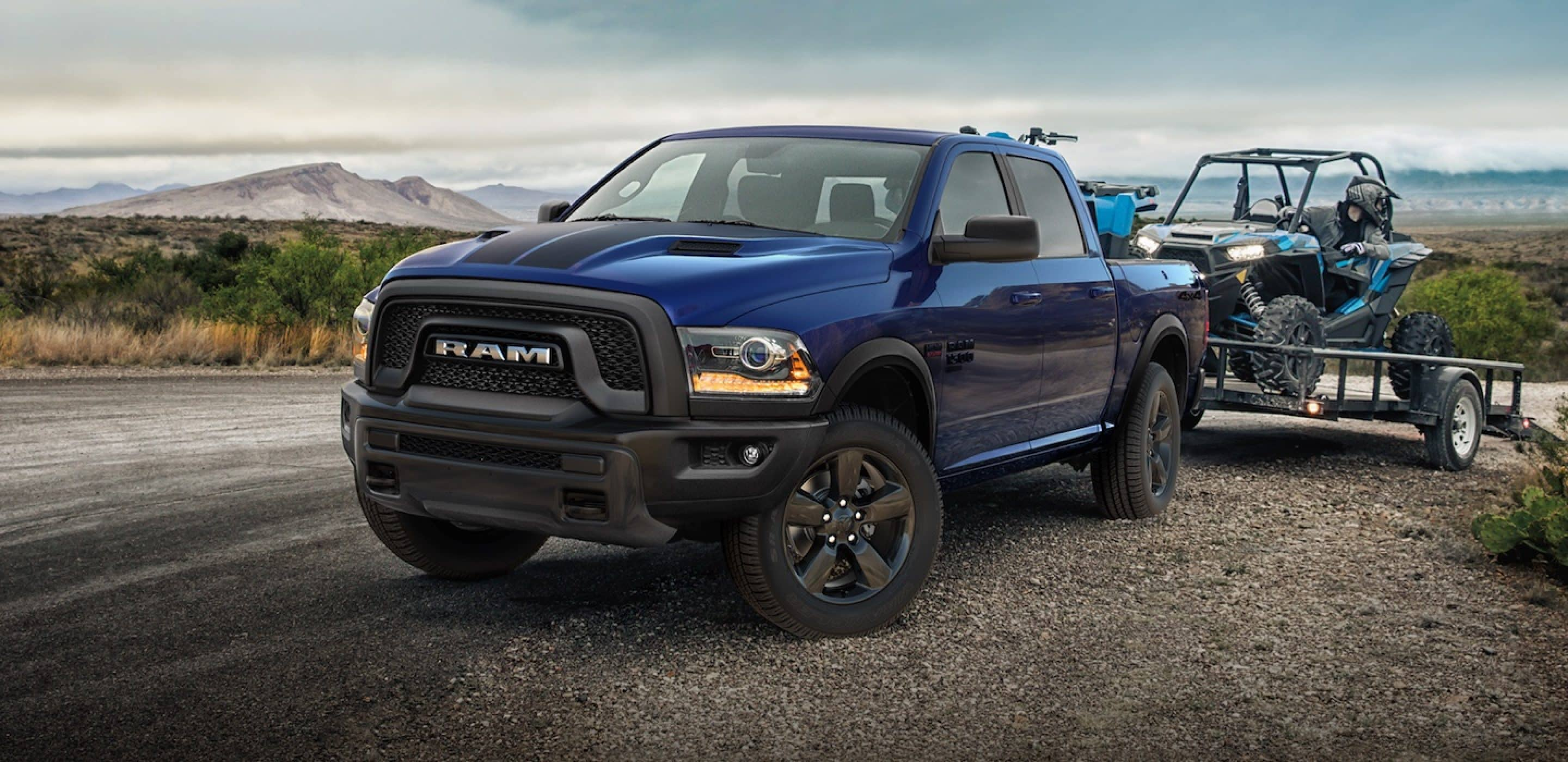
Most Compact Actuator Suspension In Brick Rigs Video
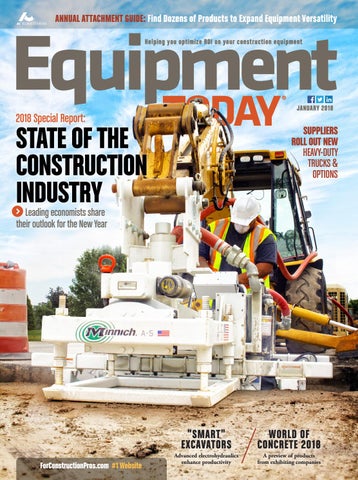
Shows one of the most common MEMS suspension designs, supporting a platform at each corner with a folded flexure. This kind of suspension provides a relatively low vertical and transverse spring constant due to the short and meander-shaped spring structures forced by the relatively narrow width of the actuator.
(8)to maintain a constant lateral spring constant, all other dimensions being equal. This additional length is accommodated, or even exceeded, by interlacing sets of double springs. Illustrations 4 b) and c) show improved spring layouts for actuators with constrained side-to-side dimensions.
The alternate designs use the maximal available length for springs but also providing the platform with a high vertical and transverse spring constant by using a double-spring suspension. Compares the spring constants and dimensions of the three different suspension systems shown. High transverse and vertical spring constants and high lateral flexibility make design 3 suitable for carrying and guiding a lens that will be fixed perpendicular to the platform’s surface. Design OptimizationTo optimize the performance of the amplification stage 14 design parameters, including suspension lengths and widths and distances between spring connections to the rigid portion of the transmission were optimized. The optimization used the analytical model, linear simulations and non-linear simulations.
Sweeping the values of single parameters in the analytical model identified its sensitivity to each variable. High influence parameters were then analyzed in Design of Experiments software JMP to optimize their values when accounting for mutual influences. A non-linear simulation was used to verify the performance of the final optimized set of parameters. Shows key dimensions of the resulting actuator used for experiments (minimum beam width of 8 μm).
Fabrication and AssemblyA Silicon-On-Insulator process is used to fabricate the amplifier and platform structure, with a 100 μm thick device-layer and 3 μm thick SiO 2 buried oxide layer. Wafers are coated with Low-pressure chemical-vapor-deposited silicon oxide, for better protection during deep-reactive ion-etching (DRIE), and gold pads are deposited via a lift-off procedure to provide electrical conduction to the underside of the PZT ceramic. The transmission, suspension, and platform geometry is then patterned into the device-layer by DRIE. The backside of the actuators (handle-wafer) is also patterned by DRIE to remove material behind the PZT connection point and the moving platform, reducing the odds of adhesive impeding moving parts. Hydrofluoric Acid (HF) is then used to etch the SiO 2 by a timed etch, followed by critical point drying. Minimal surviving feature sizes from the device layer DRIE were 6 μm, used for spring design. Due to long etching times a slight lateral overetching of 1–2 μm and some footing were observed during the DRIE process.
The actuator on the wafer is surrounded by an etching trench and automatically detaches from the wafer which replaces dicing.shows a completed actuator consisting of the PZT, the two amplification stages and the lens platform. The PZT strip has dimensions of 150 μm × 3 mm × 10 mm. Its piezoelectric coeffcient d 31 is 2.1 10 −10 C/N and when actuated at 110 V a displacement of 1.5 μm can be obtained against the stiffness of the transmission. The PZT is connected to the handle layer on one end and fixed to a movable platform in the device-layer at the other end pushing or pulling the mechanical amplifier. Silver conductive adhesive is used for the fixation of the piezo. Piezoelectric actuator motion at 80 V, a scale helps to determine the distance traveled by the platform (small scale bars: 5 μm, large scale bars: 20 μm).A comparison between the measured values for the platform-displacement and the calculated and simulated results is shown in. Is plotted in a voltage range from −100 V to 100 V.
The measured DC platform-displacement is indicated by the black squares. At ±100 V the PZT displacement is ∓1.43 μm and the platform displacement ±243 μm which equals a total platform displacement of 486 μm and an amplification ratio of 170 (all values are DC values).
The measured displacement is very similar to the calculated and simulated ones. The slightly higher displacement of the real system can be explained by the lateral and vertical thinning during fabrication.
Although the flexural lever arm, chevron, and suspension springs have nominal widths of 8,8, and 12 μm, overetching and sidewall erosion during the DRIE step leads to a more flexible structure, similar to a design with widths of 6, 6, and 8 μm. Comparison of the measured displacement of the actuator with the results of the analytical model and the simulation.An AC characteristic of the device is shown in. A supply voltage of 3 V is applied to the electrical contacts of the PZT and the frequency is swept from 1 to 800 Hz. Whereas the displacement for 3 V at 10 Hz is only 7.5 μm a distinct resonance frequency can be found at 507 Hz with an actuator displacement of 370 μm (no lens included). Although in practice the actuator will be operated below resonance, a high resonance frequency is required in order to allow accurate DC-scanning at video frequencies (10 Hz) when carrying a lens.
Experimentally, when a 0.12 g mass is added to a single actuator, natural frequency is measured at greater than 37 Hz, compared to an anticipated 43 Hz. Frequency sweep at 3 V input voltage, showing resonance peak at 507 Hz with displacement of 370 μm.In addition to the nominal actuator design, with thickness of 0.6 mm, width of 3 mm and length of 23 mm, two alternative, more compact designs were fabricated. One places the lens-platform within the amplifier (middle) and another one with the 150 μm thick piezo situated in the 500 μm thick handle layer (bottom).
For this shortest design, a stack of piezo strips could be used without increasing the dimensions of the system (up to 3 piezo strips on top of each other), while remaining within a total length of 12 mm. ConclusionIn this paper we have presented the design and fabrication of a piezoelectric actuator for miniature two-photon microscopy. The actuator consists of a PZT, a mechanical amplification mechanism and a suspended lens-platform. The mechanical amplification has been optimized by an analytical model and linear and nonlinear simulations. The entire actuator has been fabricated using a SOI process and then characterized. With an amplification factor of 170x, the amplifier is able to transform a PZT input displacement of 1.43 μm (at 100 V) into a lens-platform displacement of 486 μm. This nominal design meets the specifications needed for the integration into a two-photon endoscope probe to allow 3-dimensional imaging.
Other designs have also been fabricated that reduce actuator volume to as little as 0.6 mm × 3 mm × 12 mm.